Introduction
In the previous post we’ve seen some of the basic concepts to take into account when we are going to design a sheet metal part. However, this concepts alone won’t help us to start designing any sheet metal component. In this post we talk about the necessary rules we need to know to start designing sheet metal parts.
First, consider that the following rules are not laws. Depending on the sheet metal supplier these may vary slightly due to his capabilities and available tools. In most cases the following rules will fit for most suppliers and even some of them can go beyond these limits.
Everything depends on the sheet thickness.
We will focus on steel or stainless-steel design. The following measures are commonly used for both materials, and you can design freely with them:
Sheet thickness (mm) | 1.5 | 2 | 2.5 | 3 | 4 | 5 | 6 | 8 | 10 | 12 | 15 | 20 |
There are more available thinner, thicker, and even intermedium thicknesses but we do not recommend them for the following reasons:
- Thickness inferior to 1,5mm are difficult to weld and requires a specialized welder.
- Thickness superior to 12mm is difficult to bend and even difficult to laser cut if we talk about stainless-steel.
- Thickness superior to 20mm is difficult to laser cut in the case of steel.
Now we will focus on the geometrical proportions to respect when we design a sheet metal component. This proportions are related to the sheet thickness (we will abbreviate with “Th.”)
Geometrical proportions for a good sheet metal design
Minimum bend radius (Rmin)
Rmin = Th.
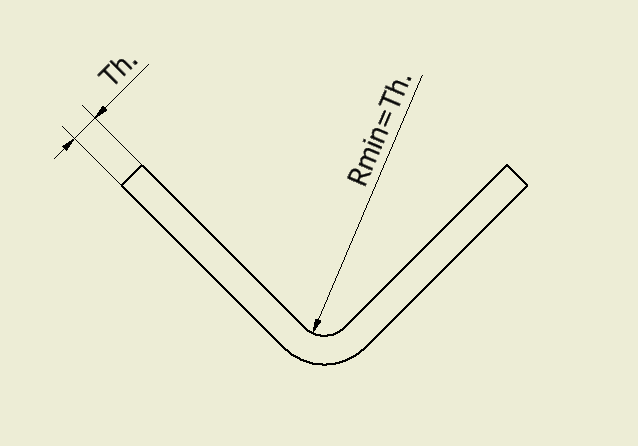
Minimum flange length (FLmin)
FLmin = 5*Th. (approx. for a 90º bend angle).
- If the bend angle is grater than 90º, the constant would be minor than 5.
- If the bend angle is minor than 90º, the constant would be grater than 5.
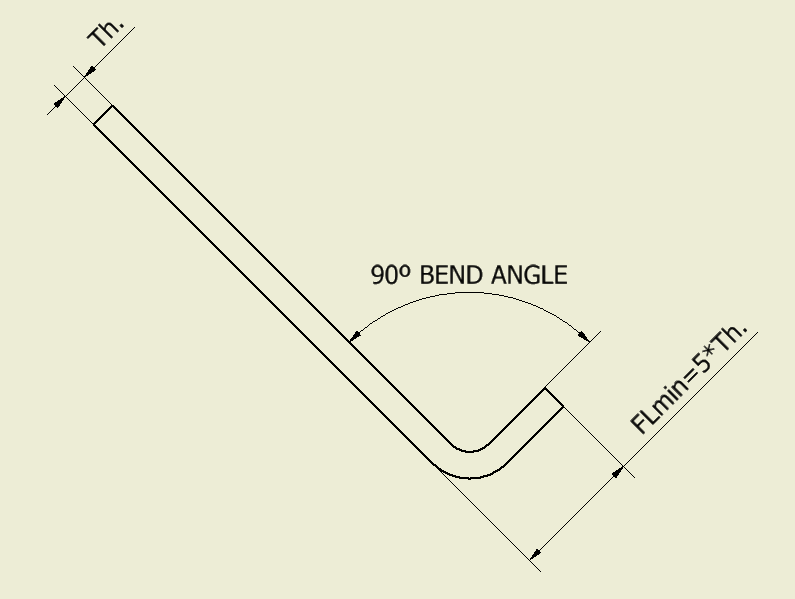
Minimum hole diameter for steel (Ømin)
Ømin = Th.
For threaded holes, this rule applies for the pre-drill diameter.
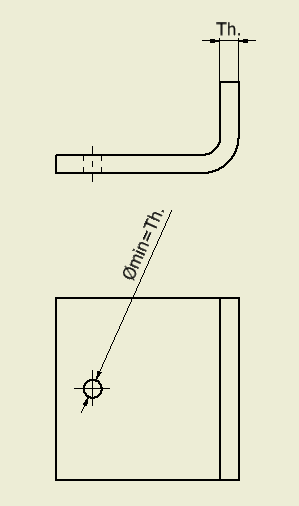
Minimum hole diameter for stainless steel (Ømin)
Ømin = 0.8*Th.
For threaded holes, this rule applies for the pre-drill diameter.
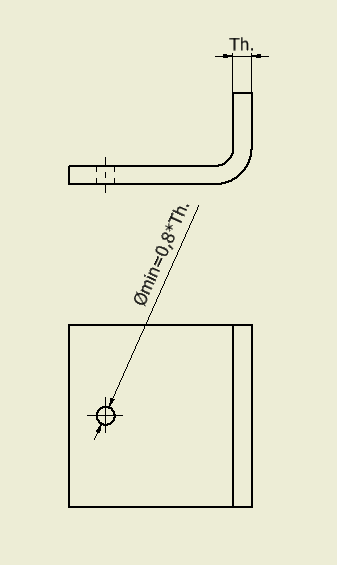
Maximum bend length
L=3 meter
Bends over 3-meter length requires big machinery. If a long bend is required, you may consider dividing the sheetmetal in half and then weld the two pieces.
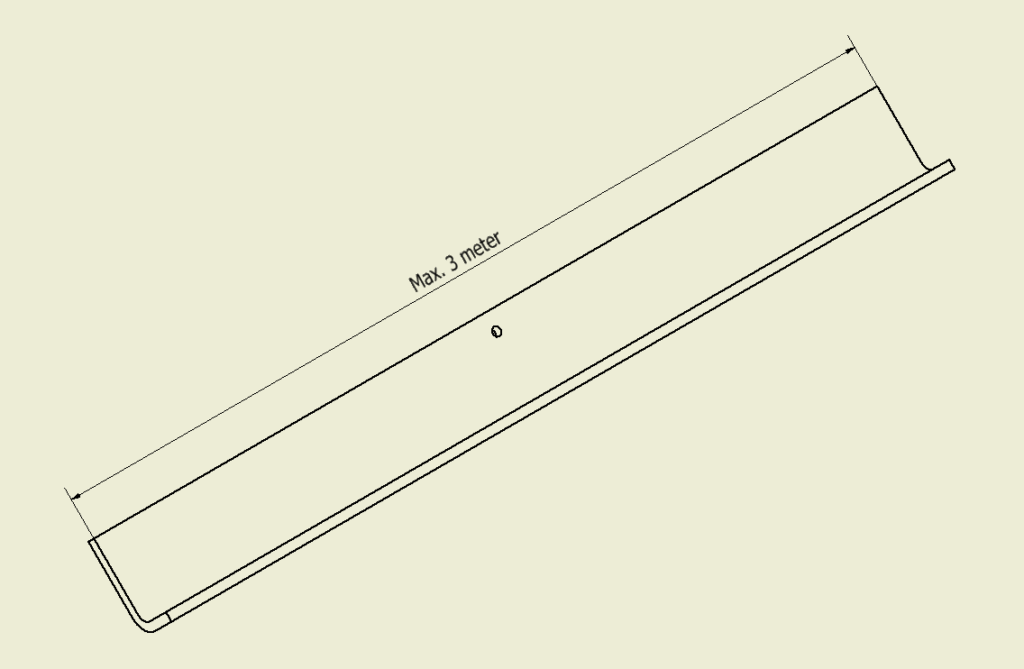
Remember, these rules are an approach to design a “there won’t be any problem to make this component”. This means you can find providers who can make products following even more restrictive rules.
E.g., Bend radius inferior to sheet metal thickness (this is very common), or even an inferior flange length than 5 times thickness.